Interim Supply Chain Management and Consultancy for the FMCG Manufacturing Industry

Excel Production Planning
Supply planning of manufactured items requires consideration of operational capacity constraints, a function that core system MRP functionality does not provide.
​
Sophisticated Advanced Planning and Scheduling solutions are available that can balance inventory requirements within capacity constraints, but they can be a costly option and require master data integrity and maintenance within the ERP solution.
​
HMS has developed and implemented integrated Excel Master Production Schedule (MPS) solutions in various businesses to manage in excess of 1000 SKUs over multiple production lines.
​
The solution supports line level capacity balancing from item level production planning, combines automation to avoid manual data transfer and utilises visual alerts to aid the user and support management by exception and includes inventory management reporting.
​
Planned over a shorter horizon than the Rough Cut Capacity Plan (RCCP), the MPS is a SKU level capacity balanced plan, typically maintained out to the horizon of the longest material supply or operational lead time, the MPS allows production of products to be planned at family level to maximise manufacturing efficiency and planned within SKU level inventory policy.
​
Maintaining an MPS also provides BoM component requirements aligned to manufacturing requirements which ensures material availability and avoids unnecessary excess material inventory or shortages.
​
Read our article 'Are Excel Planning Tools an Effective Option?'.
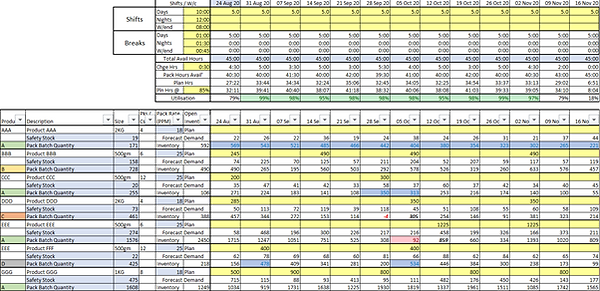